1. Poor appearance
(1). Internal stain
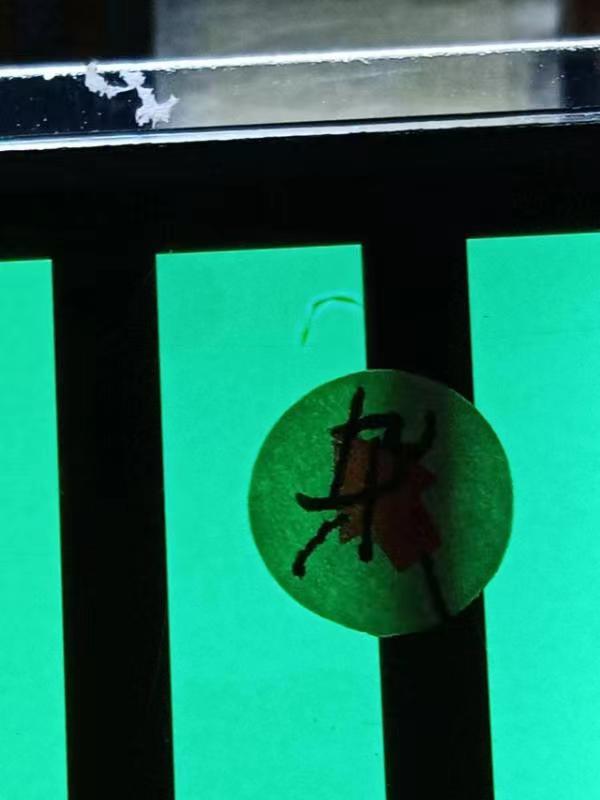
It is called black spot, stain, and fiber. It means the fiber or stain inside the LCD.
(2). Internal scratch
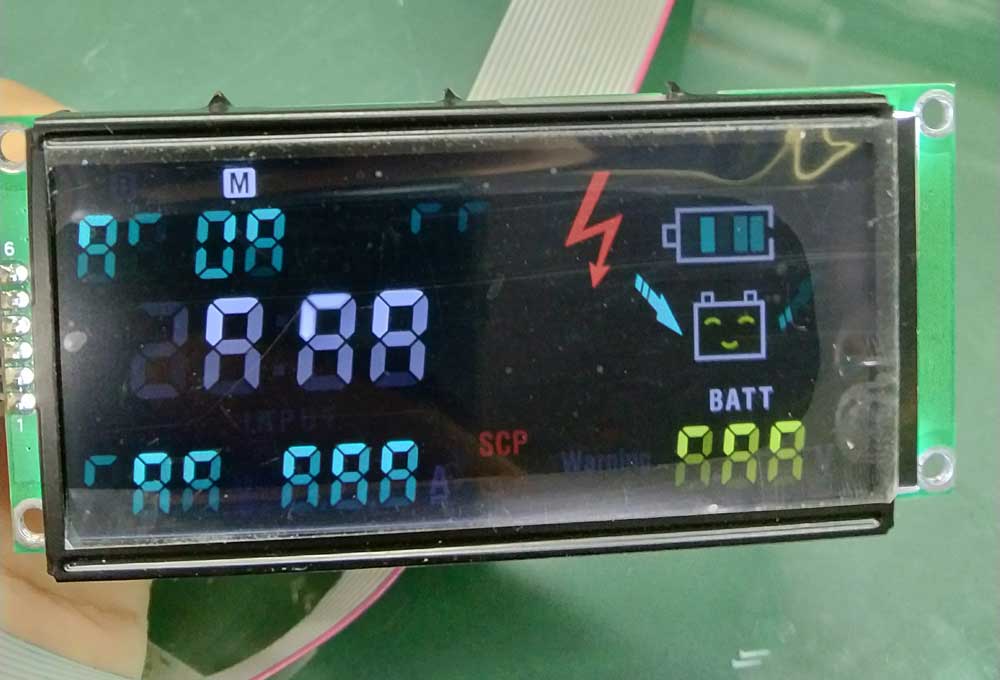
It is called a black line or a white line, and it is scratched on the surface.
(3). Color unevenness
It is called color unevenness and rainbow, that is, the color of LCD is uneven, and the rainbow in the middle or on the edge of the bar and the color stripe are uneven.
(4). Inconsistent background color
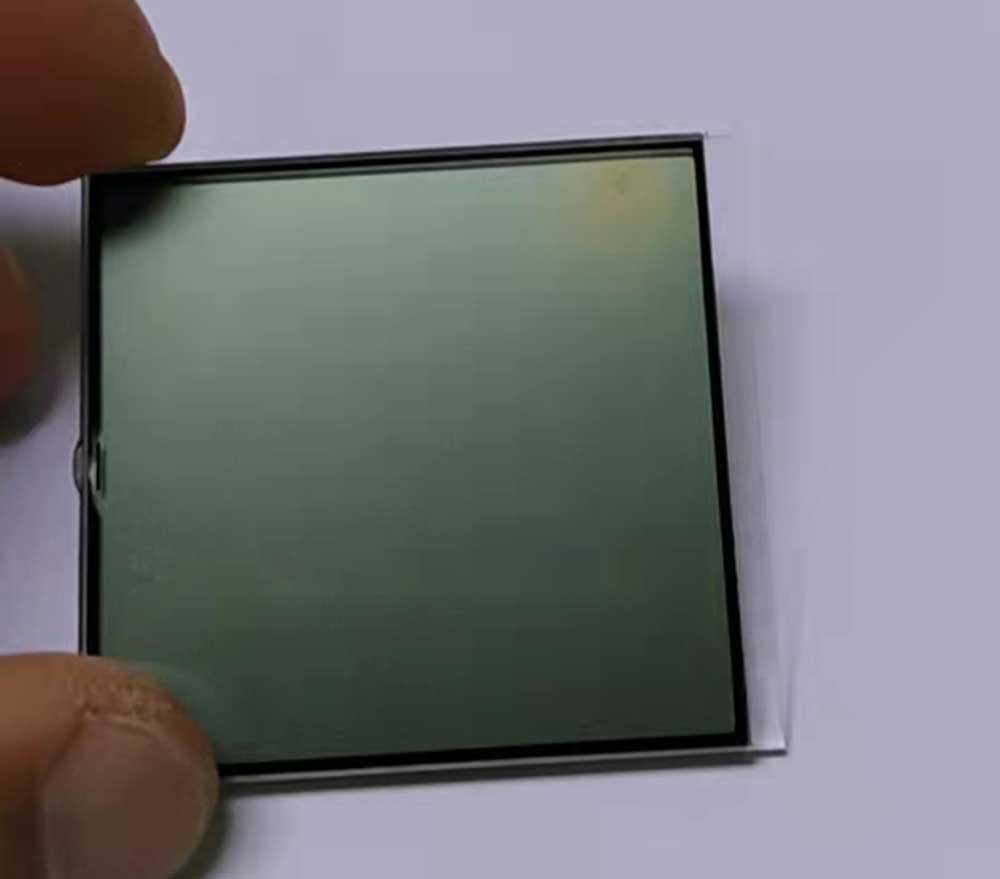
Generally speaking, the overall color of LCD differs greatly from that of other LCDs. Generally, it is not compatible with the samples.
(5). Broken
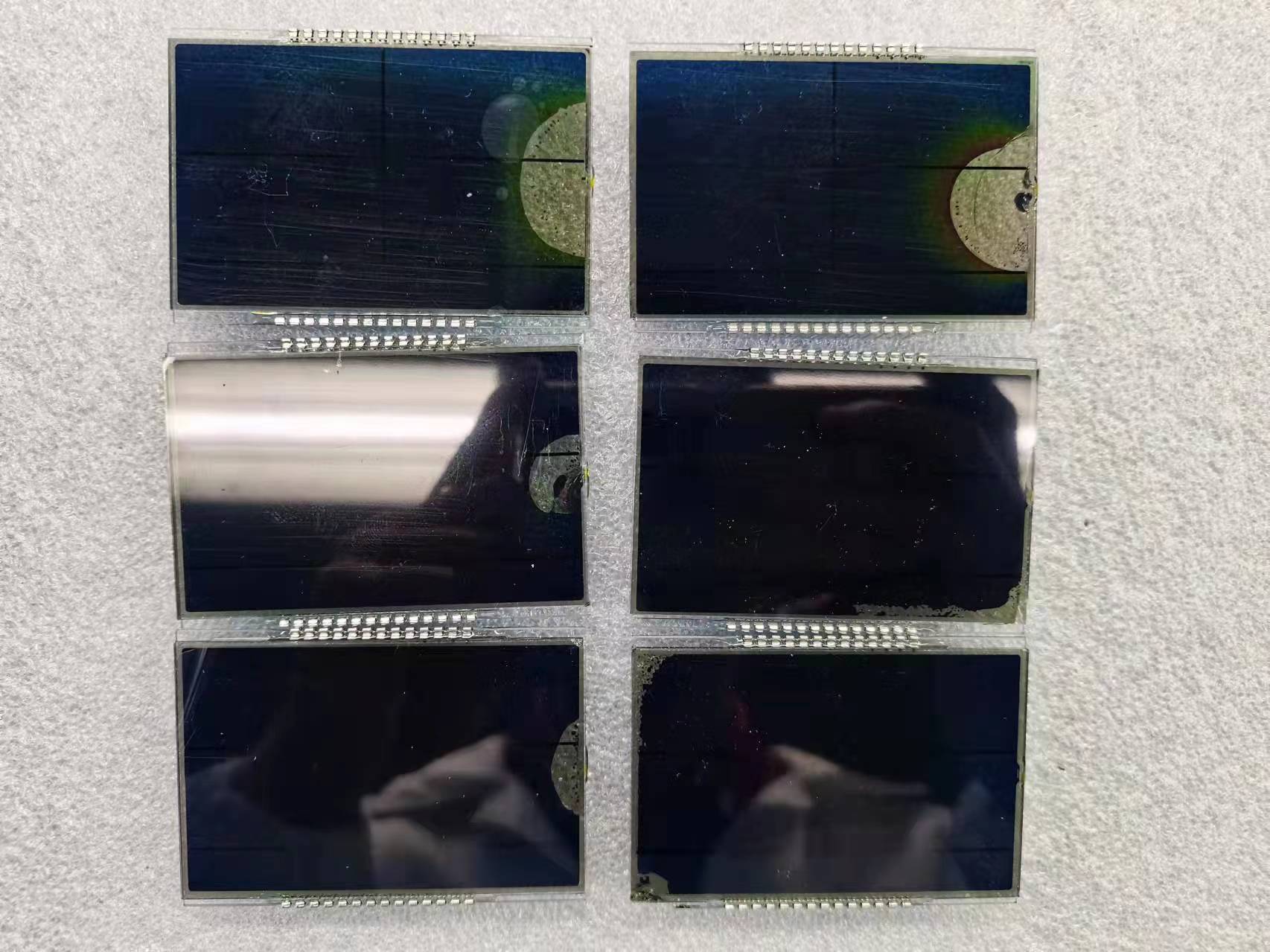
It is called broken glass. That is, the damaged part of the LCD is incomplete, including corner damage, edge damage, and conductive layer damage (that is, the side of the pin is damaged, generally due to many human factors, which may be caused by the company and customers).
(6). Poor cutting and cracking
Some protrusions or depressions are caused by Y-axis cutting and X-axis splitting.
(7). Pin scratch
The PIN side of the LCD (i.e. the conductive layer) is scratched or cut, resulting in open circuit and poor conductivity. It is often caused when it is repaired.
(8). The polarizer is scratched and punctured
It is called “mirror blur”. That is, the polarizer is damaged or damaged by hard hands such as blades (caused by improper placement and use by customers).
(9). Stripes on the polarizer
There are stripes on the polarizer, which can only be seen when the backlight is lit. It is caused by the penetration of alcohol or acetone when we are wiping the conductive layer with alcohol or acetone.
(10). No protective film
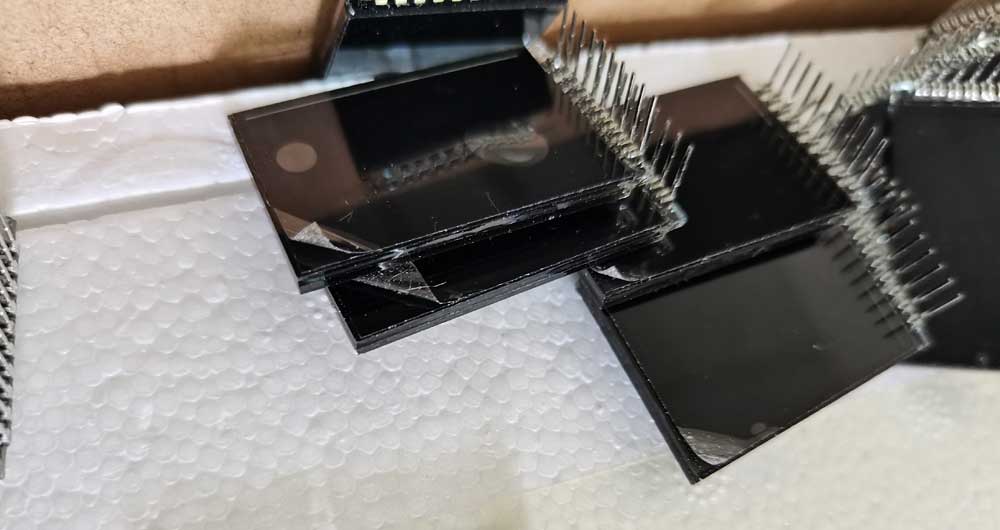
The protective film on the surface of the polarizer is torn off. Generally, it is caused by careless packing.
(11). Polarizer bubble
There are small bubbles on the polarizer on the LCD surface after mounting, which affects the usability of the LCD. It is caused when the polarizer is assembled on the ITO glass.
(12). Reverse pasting
It is called wrong pasting, which means that the polarizer is pasted reversely, such as the front polarizer is pasted on the back of the LCD screen.
(13). Bumps and fibers
Dust, fibers, and other pollutants fell into the LCD surface, or the polarizing part itself was dirty during the mounting.
(14). Polarizer corrosion
The polarizer changes color or shape due to a chemical reaction with some liquid.
(15). Mixed materials
Mixed materials of different types and performance, mixed materials of different models with different versions, mixed LCDs of other manufacturers, and mixed LCDs of different periods.
(16). Backlight bleeding
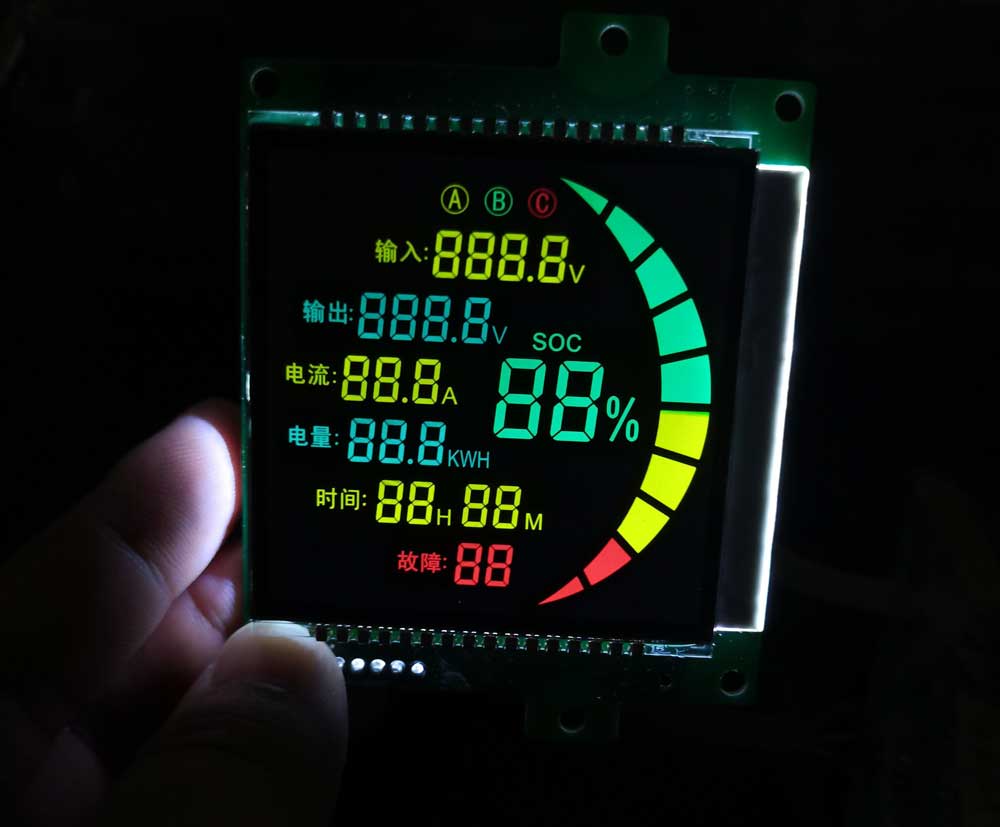
Generally, this is a design problem. Sometimes, LED backlight made is bigger than it should be. More often than not, it is caused by the shortage of light-blocking film.
(17). Liquid crystal leaking
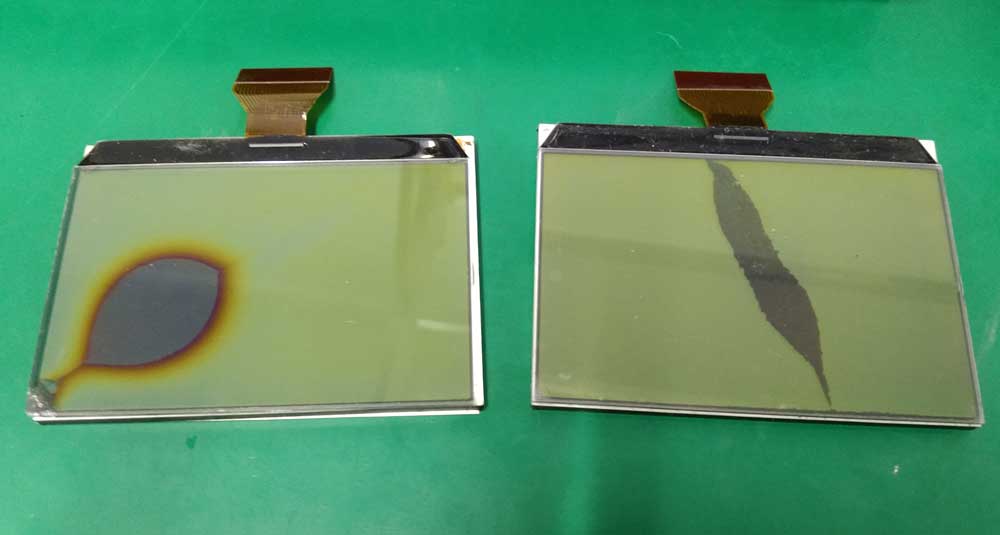
Liquid crystal leaking from broken glass. LCD display is fragile, and be careful when moving it.
2. Poor electrical property
(1). Short circuit
It is called long-ringing, ringing, short-circuit and light leakage. Because the cables that should not be connected to the LCD are connected, and with the large current being magnified infinitely (the electrical alarm will ring), some of the segments in the LCD are fade or missed.
(2). High current
The display content on the module is weak and fuzzy or the battery is depleted quickly. If it is DC power supply, it is normal that the current is high during electrical measurement.
(3). Open circuit
It clauses fewer segments, missing segments, and hyphenation. Generally, It is caused byscratched ITO film.
(4). Insufficient etching
It is called black spots or multi spots, and a extra segment or pattern is added to the display content.
(5). Excessive etching
It clauses the letter smaller and deformation, and some segments are missing from the display content.
(6). Light color
It is usually caused by the lower driving voltage. The color of the segments will deepen if we increase the driving voltage.
(7). Ghost shadow
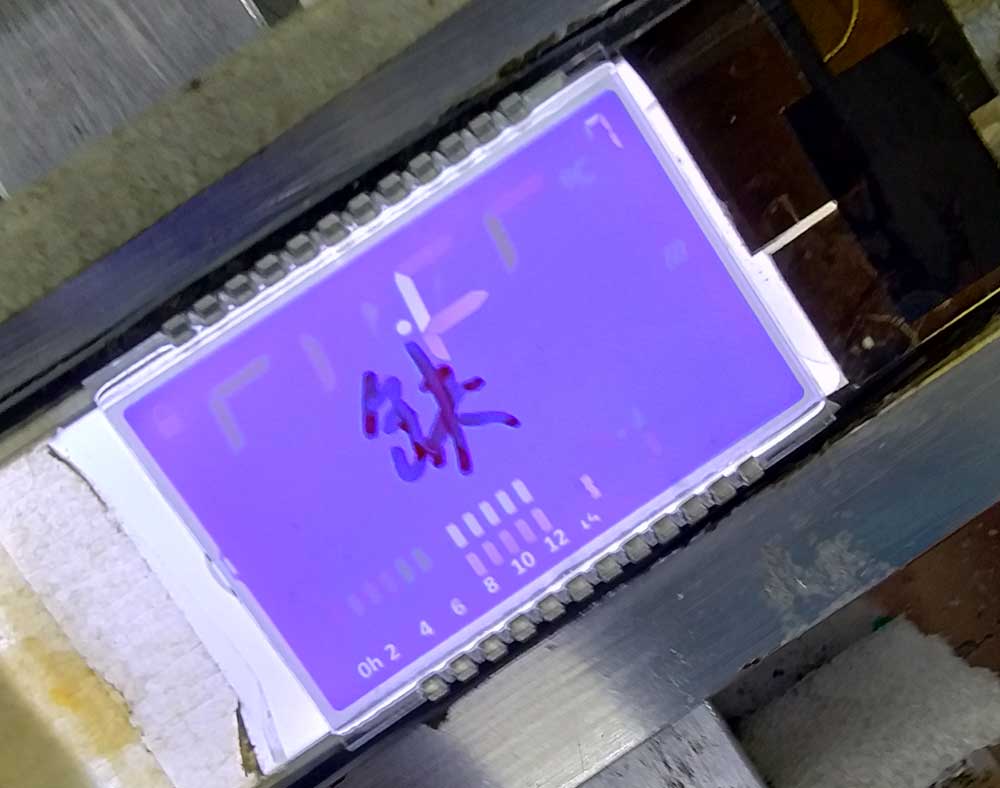
That is, the color of segments is deeper than the sample when compared with the sample in the same visual direction under the same voltage. The segments that should not appear are displayed on the display content of LCD. They can also be seen vaguely even when they are not turned off, affecting the contrast ratio.
(8). Light leakage
Some segments are lighter than others. The degree of the ghost of segments that are not displayed is inconsistent, that is, the segments are not uniform.
(9). Poor conductivity
It is called flicker, segment flicker, segment ambiguity, poor contact, shaking, incomplete display, half display, missing segments… The reason is poor conductivity. During electrical testing, the display of a few segments are unstable under normal voltage, and the display content is blurred or not showed. However, when it is tested on the electric tester and the voltage is raised, it can normally display, which is different from “open circuit”.
(10). Uneven Surface
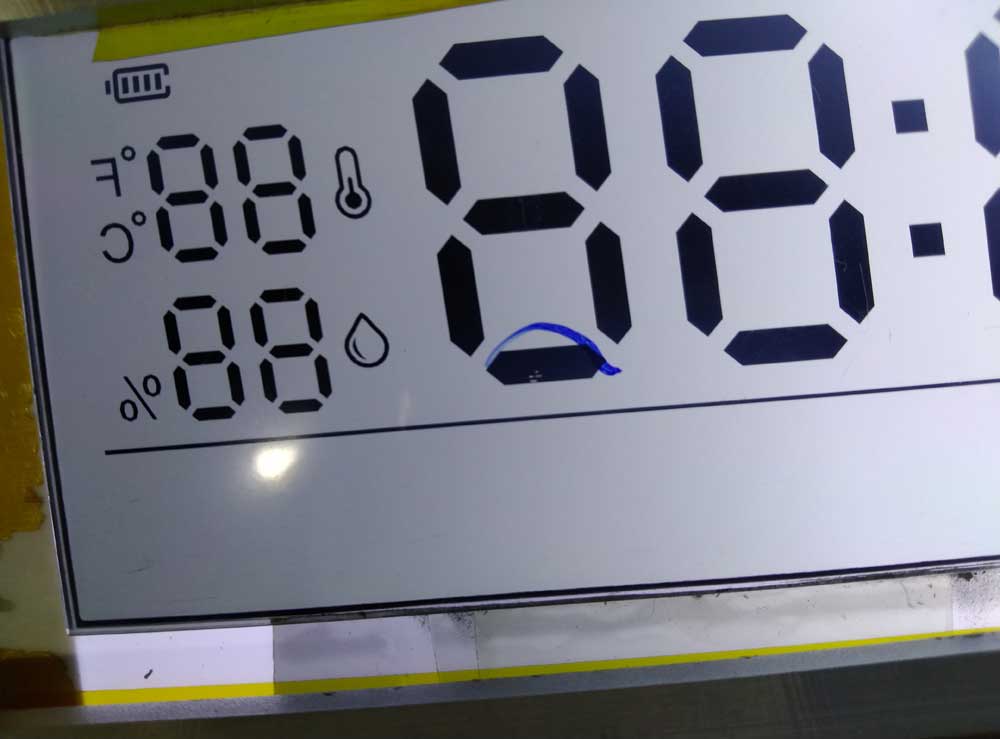
Uneven grayscale, some display segments missing, white spots, black spots, stains… During electrical testing, there will be white or black spots on the view area, and these spots will generally shrink or expand with the frequency and voltage of the electrical testing machine. Therefore, it is important for LCD display factory to test every LCD screen before the shipment.
(11). Display content missing
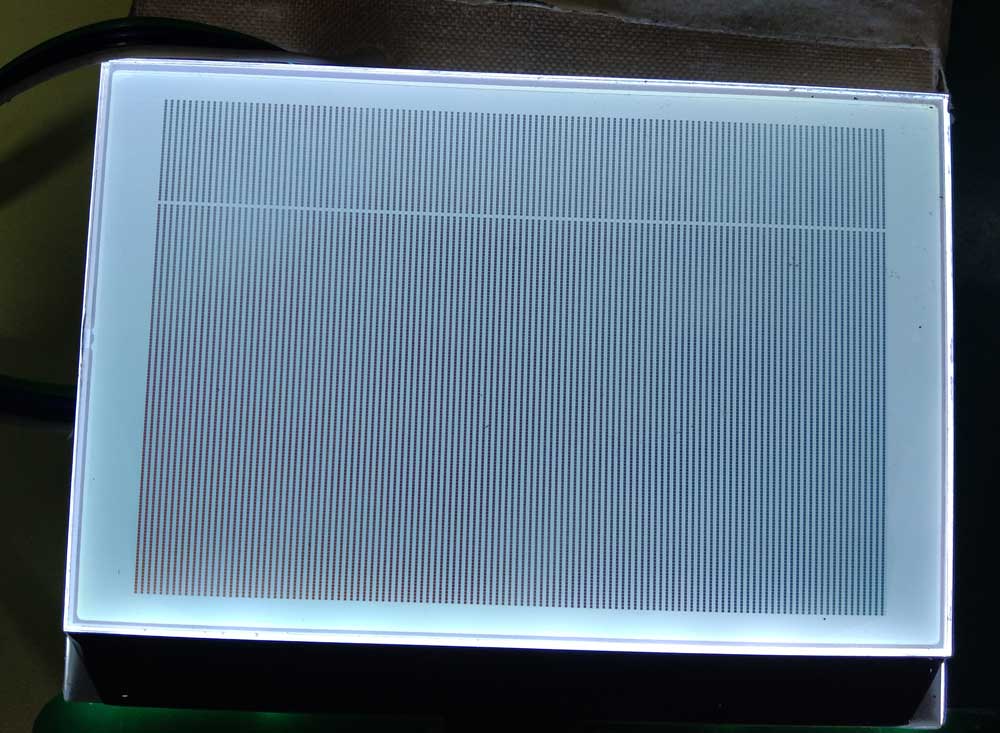
Some segments or dots missing from the view area.