1. Introduction of Light Guide Plate
The main material of light guide plate is an optical acrylic sheet whose chemical name is polymethyl methacrylate (PMMA) and its weight is 1190 KG per cubic meter. Transparent acrylic sheet is widely used because of its high light transmittance and strong impact resistance. The acrylic sheets in the market nowadays have huge differences among various processes of different manufacturers. Although recycled acrylic sheets are much cheaper, they easily get yellow and have a poor transmittance. The acrylic sheets which are produced into light guide plates should be anti-oxidized and have more than 92% transmittance. The light guide plate is a transparent acrylic sheet which has been specially and scientifically processed and has light sources installed on the sides, which could be used in traditional fluorescent tube lights, LED lamps, CCFL(cold cathode fluorescent lamps), and so on. When the power is on, the acrylic sheet will emit a bright and uniform soft light.
Light guide plate has been widely used.
Application products of light guide plate: super-thin light guide lightbox, light guide indicating plate, luminous photo frame, LCD backlight, super-thin film player, and so on.
The materials which can be used in the boards of light guide plate are stainless steel, aluminum, wooden frame, plastic, and so on.
The features of light guide plate are super-thin, low power consumption, uniform brightness, comfort visual, and attractive appearance.
Application fields: commercial centers, supermarkets, banks, chain stores, hotels, airports, bus stations, train stations, tunnels, subway stations, trains, elevator advertising displays, exhibitions, electrical products, LCD backlight, backlight instrument and so on.
2. The Classification of Light Guide Plate
Light guide plates can be classified by the shape, the production methods, the functions and so on. So far, there is no uniform classification.
1. Light guide plates could be divided into flat light guide plates and wedge light guide plates according to the shape.
Flat light guide plate is that the light entrance looks like a rectangular.
Wedge light guide plate is that the light entrance looks like a triangular which one side is thick and one side is thin.
2. Light guide plates could be divided into edge light guide plates and bottom light guide plates according to the production methods of light lattice .
Printed light guide plate is that light guide lattice points are printed onto the back side of light guide plate. And it is divided into IR printed light guide plate and UV printed light guide plate.
Non-printed light guide plate is that light guide lattice points take shape while light guide plate is formed. And it is divided into chemical etching, precision machinery characterization method (V-cut), photolithography (Stamper) and internal diffusion.
3. Light guide plates could be divided into edge light guide plates and bottom light guide plates according to the position of light source (such as LED lamps).
Edge light guide plate is that light source is placed at the edge side of light guide plate.
Bottom light guide plate is that light source is placed at the bottom side of light guide plate.
4. Light guide plates could be divided into injection molding light guide plates and cut forming light guide plates according to the production methods.
Injection molding light guide plate is that optical PMMA particles are injected into high temperature and high pressure injection molding machine and cooled into shape.
Cutting Forming light guide plate is that original board of optical PMMA is cut into various shapes.
The following image is an oil-printed light guide plate.
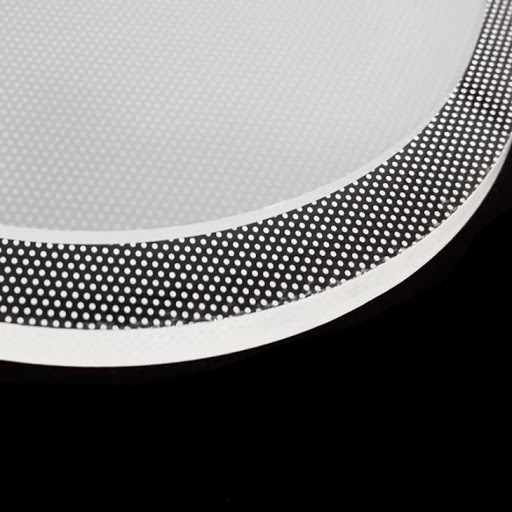
This is an image of a light guide plate made by a dedicated mold.
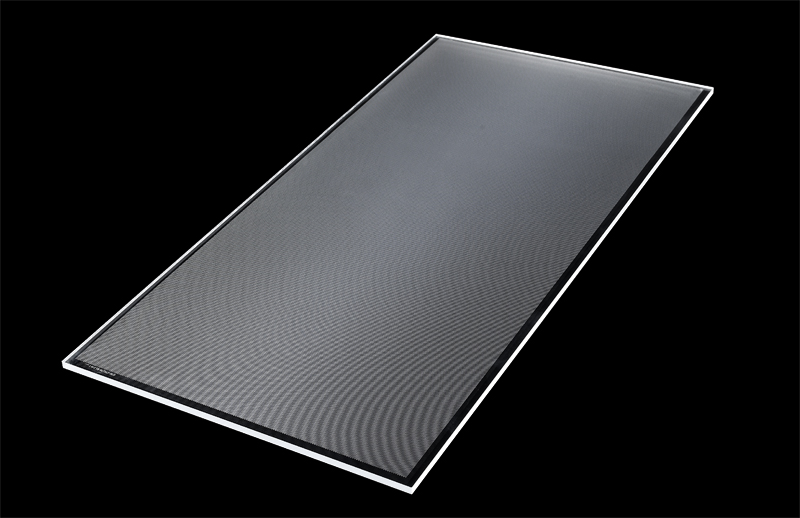
3. An Analysis Of The Light Guide Plate Production Technology
Light guide plate is an important part in backlight industry and the LCD industry. This article is going to discuss the material of light guide plate and the drying methods of printing ink.
1. Material: Nowadays, the PMMA is the most widely used material in backlight industry and LCD industry. PMMA (POLYMETHYL METHACRYLATE), which is also known as acrylic or plexiglass, is poison-less and has good chemical stability and heat resistance which can be used in the production of tableware, sanitary ware and so on. PMMA won’t be broken into pieces of sharp fragments. The United States, Japan and other countries and regions have to make a mandatory provision in the law that the architectural glass of schools and kindergartens must employ PMMA resin. Also, it has been extensively used in outdoor architecture project of Beijing Olympic. But due to the inherent shortcoming that low surface hardness, low impact resistance, poor deformability and so on, some backlight manufacturers and LCD manufacturers begin to look for the alternative to PMMA. Nippon Zeon (Japan) has promoted a new material Zeonor cyclic olefin polymer (Cycio Olefins Polymer, COP) for a few years. It has a couple of selling points that are low specific gravity and low water absorption. Its capacity hasn’t reach economies of scale because Zeonor only has been launched for a few years and the unit price of Zeonor is almost four times as PMMA’s. It is purely a joke that Zeonor will be applied on a large scale in our low-profit era at present.
2. It is divided into natural drying, IR (Infrared) drying and UV (ultraviolet) drying according to the drying methods of printing ink.
Natural drying is only applied in products whose quality is less strict with printing ink effect. Let us see the comparison with IR and UV.
Drying methods | IR (Infrared) | UV (Ultraviolet) |
Specific methods | Heated in a container | Irradiated by ultraviolet |
Advantage | Good reflection, high brightness and good adhesion | Easy to control the quality because of low brightness and fast production |
Disadvantage | Printing ink is not stable because of high brightness, and the capacity is limited | Low brightness and light guide lattice point is easy to fall off |
4. The Process Of Light Guide Plates Manufacturing
In order to understand the manufacturing process of light guide plate, we should know the parts and materials which are necessary for the light guide plate in advance.
1. The necessary materials and tools
a. Injection molding: optical PMMA particles, inks
b. Cutting forming: optical PMMA plates, inks
2. Optical PMMA particles and plates:
No matter what kind of manufacturing plan is proceeded to produce the light guide plate, the most important and original material is optical PMMA (POLYMETHYL METHACRYLATE), which is also known as acrylic or plexiglass. And it can be divided into PMMA particles and PMMA plates. The MMA monomers which are extracted from petroleum have been chemically processed to make optical PMMA particles. The optical PMMA particles which can be used by injection molding have been made into optical PMMA plates by method of Casting or Injection. There are some famous PMMA manufacturers, such as: (Japan) Mitsubishi Rayon, (Japan) Sumitomo Chemical Sumitomo, (Japan) Asahicasei, (Japan) Kula Lei Kuraray, (Taiwan) Chi Mei chemical, (Korea) World and Sehwa.
3. Ink: It is divided into ultraviolet (UV) and infrared (IR).
4. There are three main steps of cutting the light guide plate.
Step one: polish the luminous surface of the acrylic plate and then cut the acrylic plate into the form we need.
Step two: make the light guide lattice points according to the design.
Step three: clean the acrylic plate and then print the light guide points on it. Finally, dry the plate by infrared or ultraviolet.
5. Injection molding light guide plate is divided into printed light guide plate and non-printed light guide plate, whose process is basically the same as the casting mold. Non-printed light guide plate is that light guide points which have been designed are cast in the mold, and both light guide points and light guide plate are done in the final process of injecting mold. Printed light guide plate is that light guide points are printed after the acrylic plate has been injected.
Here, let’s see some photos in our factory.
These are the original acrylic plates which are very large, about 3.5*1.5 meter. The common specifications of the thickness are 1.0 mm, 1.5 mm, 2.0 mm, 2.5 mm,3.0 mm, 3.5 mm, 4.0mm, 5.0mm.
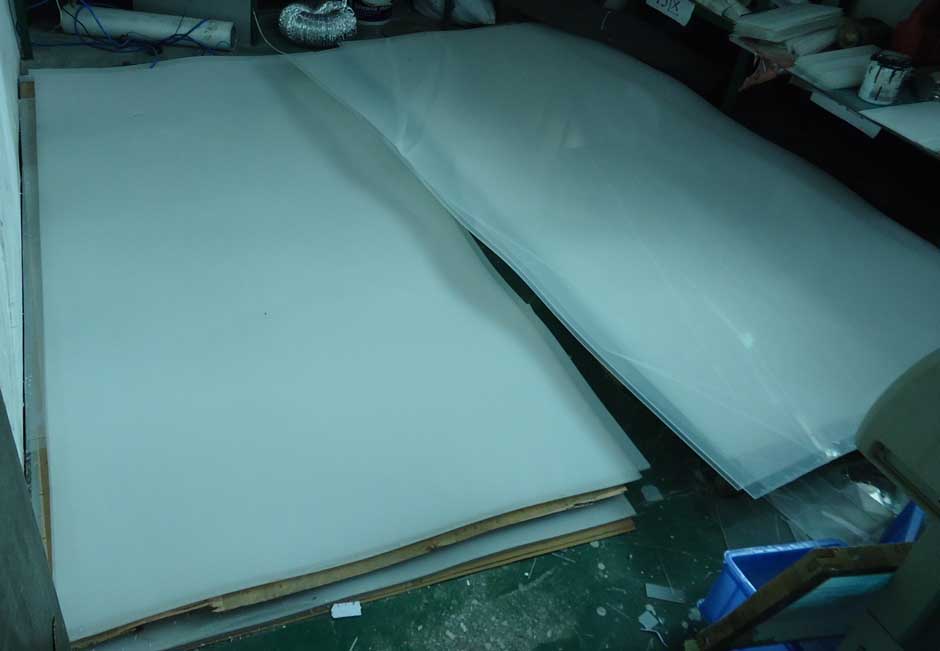
This is our new cutting forming machine for acrylic plates.
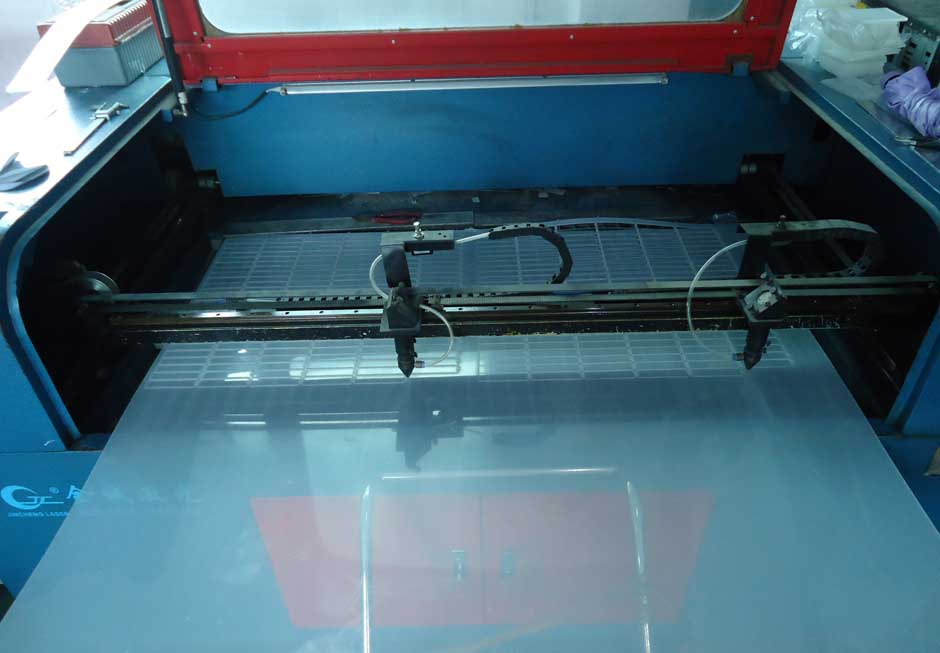
This is a front view picture of a working cutting forming machine.
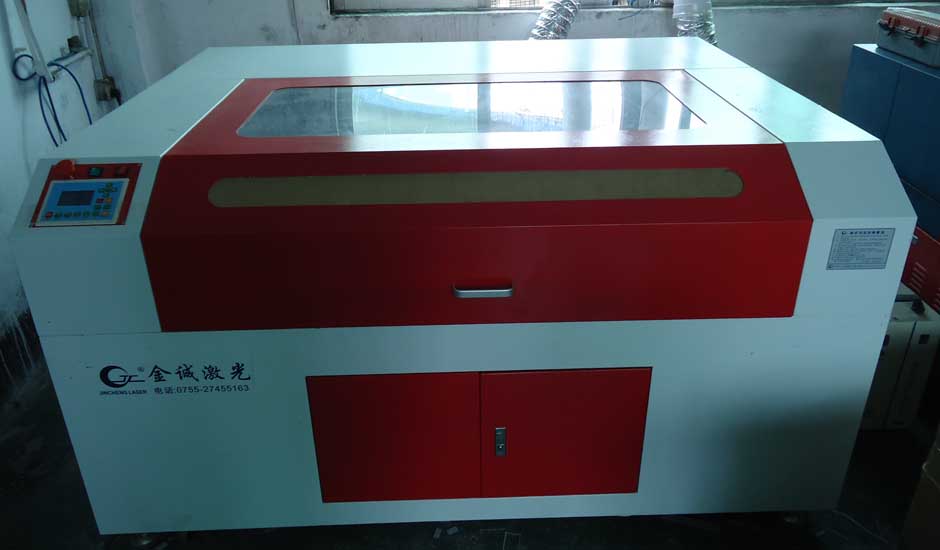
This is a side view picture of a working cutting forming machine.
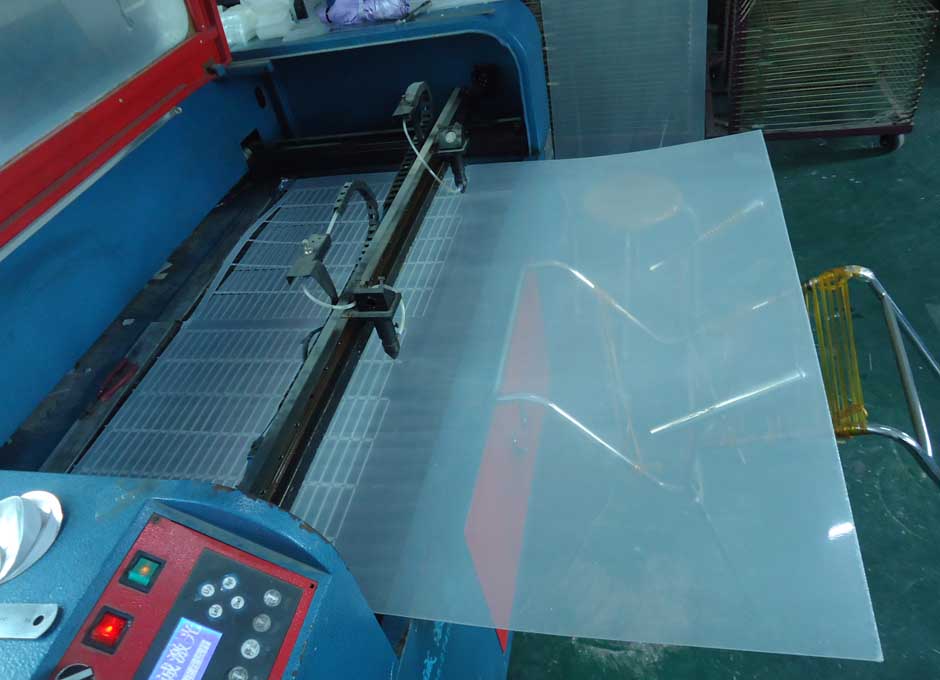
The light guide lattice points we design for the acrylic plates are carved into this transparent plate. And then light guide lattice points are printed on the surface of acrylic plates by silk-screen printing.
We often hear from our customers complain about why they need a dedicated plastic mold for a LED backlight. A dedicated light guide plate mold at least costs one thousand dollars. In fact, it is quite necessary. It not only can make light guide plates into irregular shapes and keep the shape the same from beginning to the end, but also increase the light transmittance and enhance the brightness.
We can see that there are some dedicated light guide plate molds in the photo. In fact, they are very heavy and made from steel. I have tried to lift one up but didn’t succeed.
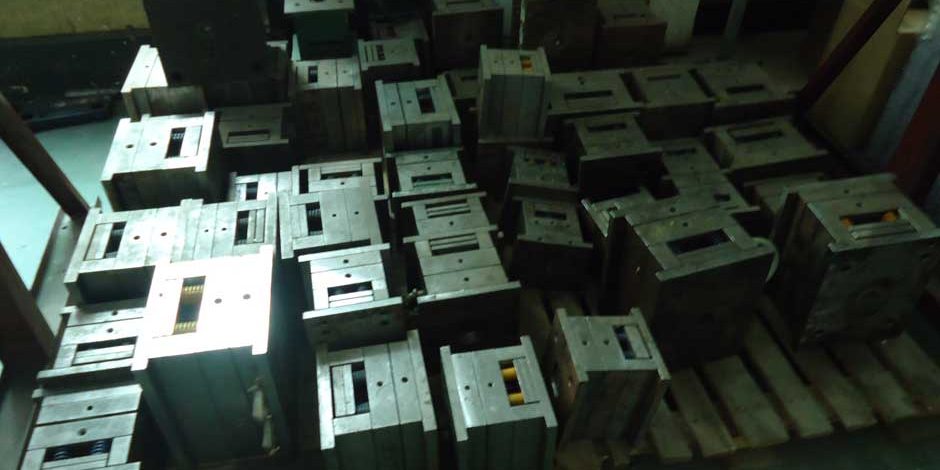
This is the injection molding machine of making light guide plates, it is pretty huge and has a very high working efficiency.
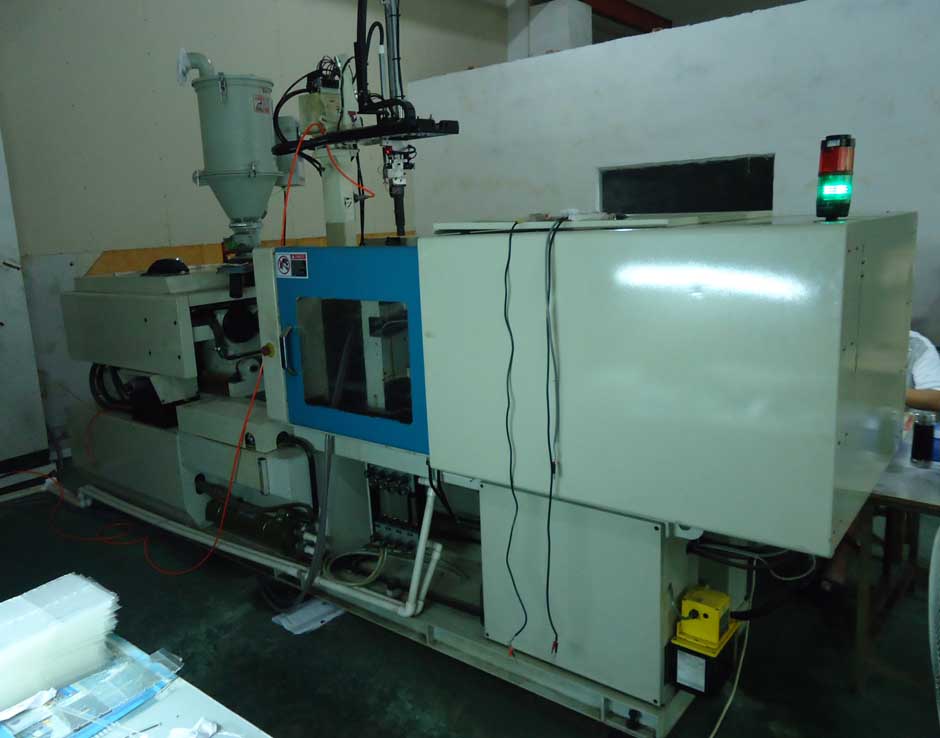
5. High Luminous V-cut Light Guide Plate Has Been Widely Used
The technology of high luminous v-cut light guide plate has been widely used in laptop computers.
The technology of v-cut light guide plate which is applied in backlight module is very popular in laptop computers nowadays. Its main structure is that a prism which has been micro-machined is installed on the light guide plate and one downward zigzag prism sheet replaces upward two prisms. It not only reduces the cost, but also effectively increases 30% of luminance.
Compared with the structure of two upward prisms, the v-cut light guide plate with the structure of one downward prism has more than 30% light efficiency. But its view angle correspondingly disappears. Fortunately, it will not affect the laptop computer, but can protect its privacy, though the pass rate is relatively low. For example, most of technology leading Japanese manufacturers with v-cut technology only have 80% pass rate, and the old technology has more than 95% pass rate. And the pass rate is impossible to skyrocket in a short time, so the cost is very difficult to decrease effectively. Because of excellent light efficiency performance, the technology of v-cut light guide plate has been gradually adopted by high-end laptop computers. For example, there are more than 40% laptop computers that adopt v-cup technology in Korea, and the technology has been widely used for a few years in Japan. However, although the v-cut light guide plate has been widely used, backlight module manufacturers still face quite a few patent restrictions because these patents are mostly owned by Japanese manufacturers. If we can’t break the new technical obstacles on our own, we have to obtain authorization by purchasing patents in order to meet the requirement of the market.